A warehouse can hold all kinds of inventory until it’s time for distribution. From receiving to shipping, the storage process in a warehouse involves multiple stages – and each one is essential to efficiency.
Streamlining these steps can help to keep your facility organised, cut operational costs, reduce the risk of errors and boost overall productivity.
Here, we explain each warehouse storage process and its best practices so that you’re equipped to optimise your operations. Keep reading to learn how to handle items smoothly from start to finish.
1. Receiving
Receiving goods is the first step in the storage process of any warehouse. It involves the delivery, unloading and forwarding of cargo for safekeeping.
At this critical stage, your warehouse must make sure it receives the right goods, in the right numbers, of the right quality and at the right time.
Why?
Because you’re responsible for maintaining these items from their receipt to their shipping.
Errors in receiving can cause discrepancies in inventory records and difficulties in order fulfilment. To avoid these issues, you’ll have to ensure all inventory arrives in the correct quantities and is in suitable condition.
That’s why you need a structured receiving process that ensures an accurate stock count and ideal inventory levels. Ultimately, the goal is to intake all inventory efficiently and correctly.
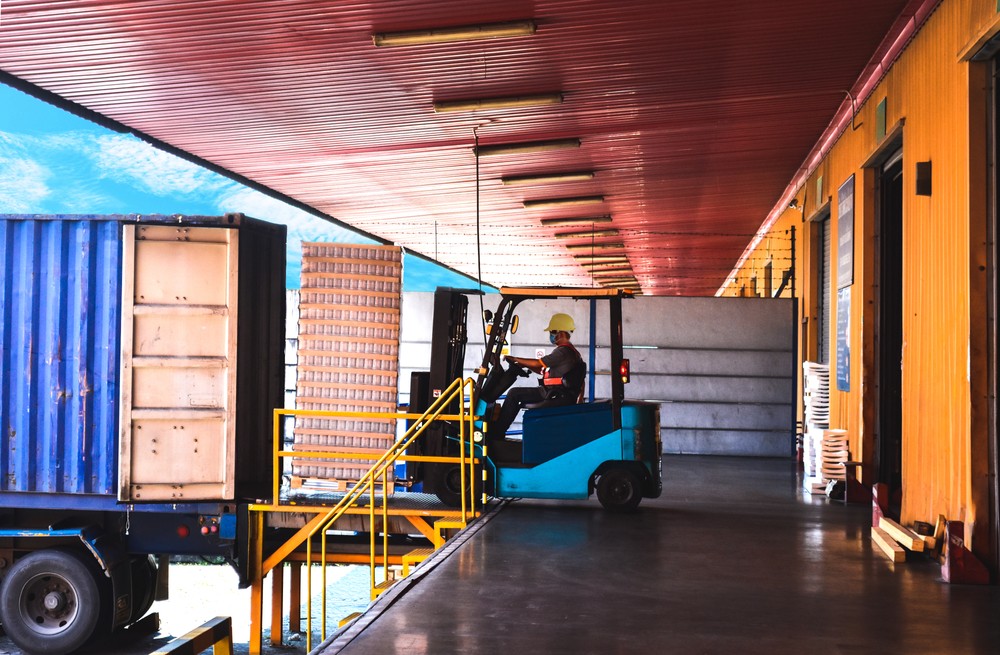
Top tips for receiving
- Arrange deliveries with respect to available manpower and space.
- Use a reliable system to count and inspect goods, cross-referencing what was ordered with what was received.
- Take advantage of technology like barcode scanners to accelerate processing.
- Implement a Warehouse Management System (WMS) that automatically updates inventory levels and alerts relevant workers in real-time.
- Adopt a clear procedure for managing order discrepancies and poor-quality items to help resolve problems faster.
- Use power pallet trucks and conveyors to unload items and clear receiving docks more efficiently.
Putaway
Putaway is next. At this point, goods are moved from the receiving dock to the designed warehouse storage space by workers alerted on the receipt of inflow.
Depending on your unique operations, you can use various putaway approaches based on factors like product types, SKUs and purchase orders.
Whichever method you choose, a streamlined process makes each consecutive inventory batch easier and faster to put away. It also maximises storage space efficiency and reduces the risk of losing or misplacing your items.
Ultimately, these benefits mean you’ll need fewer human and technological resources.
Top tips for putaway
- Standardise all putaway processes for consistency and accuracy.
- Implement a WMS that automatically directs workers to the right storage area based on item demand and available space.
- Use technology like RFID and barcode scanners to speed up putaway and help workers to identify and find products later.
- Store high-demand items in highly accessible areas to cut down on retrieval time.
- Design a zone-based putaway system that allows several workers to put away items at the same time in different locations.
With an optimised putaway process, you can transfer goods from the unloading bay to the correct storage area in a quick, simple and logical way.
Storage
Now you’re ready to store your goods in their optimal locations.
Your warehouse storage process should make full use of all available room. So, think long and hard about how to use the facility’s floor plan most efficiently (we recommend maximising vertical storage space as much as possible!).
This storage process in your warehouse can also involve specific timeframes. You’ll need to consider when items will sell and how long they can stay in the warehouse – because it’s rarely indefinite.
Top tips for storage
- Implement software that automatically assesses your warehouse storage utilisation and monitors key KPIs to determine its efficiency.
- Use a slotting optimisation system that helps allocate the most suitable storage area for incoming cargo.
- Maximise vertical space with a custom pallet racking for your facility and its inventory.
- Monitor how many items you are storing while sales trickle in. That way, you’ll know when it’s time to restock.
Picking
Picking is the process where warehouse goods are chosen and gathered to fulfill customer orders.
It is typically the most costly part of warehouse operations due to the labour-intensive tasks involved, which contribute significantly to operating expenses.
Beyond costs, the picking process directly affects customer satisfaction and, in turn, your brand’s reputation.
That’s why this process must be carried out carefully to ensure the correct items are delivered to their destination on time.
Top tips for picking
- Use Automated Guided Vehicles (AGVs) or Autonomous Mobile Robots (AMRs) so workers can pick orders at the same time, minimising human error and speeding up the whole process.
- Implement WMS software for real-time inventory visibility.
- Use voice and light-directed systems to guide pickers on optimal routes and help them find items faster.
- Choose the right picking method for your business to lower operational costs and boost productivity. Options include batch picking, zone picking and wave picking.
Packing
The packing process involves preparing goods from a sales order so they can be shipped to the customer.
This is a precise task, as workers must minimise the risk of damage to warehouse items and, ultimately, your brand’s reputation. After all, no one’s impressed if an item arrives broken, dirty or faulty!
Using the appropriate packing materials and procedures will help to ensure items reach their destination intact.
To manage weight and reduce associated costs, your packaging should also be lightweight and easy to handle.
Top tips for packing
- Use an automated system that can confirm the optimal type and amount of packaging for every order, based on factors like its dimensions and weight.
- Standardise the packing process with detailed guidelines on the procedure and materials used.
- Label every item clearly and correctly.
- Use packing materials carefully to keep the weight and size of packages within limits.
- Adopt a strict package quality control system to examine, flag and resolve packing mistakes before any order is dispatched.
Shipping
Shipping is the last step, as it’s all about moving goods from your warehouse to their final destination. It’s rare for a warehouse to have an in-house delivery team. Instead, most partner with larger couriers like DHL, UPS, and FedEx to ensure safe delivery.
For shipping to be considered successful, the correct order must be dispatched to the right customer, transported via the most suitable mode and delivered on time.
This is easier said than done. Obstacles like goods shortages, human error, machine failure, order fulfilment costs, poor real-time visibility, courier difficulties, and other issues can all get in the way.
Moreover, if the order isn’t handled correctly during previous processes like picking and packing, shipping can be delayed.
Here are some ways to support efficient shipping:
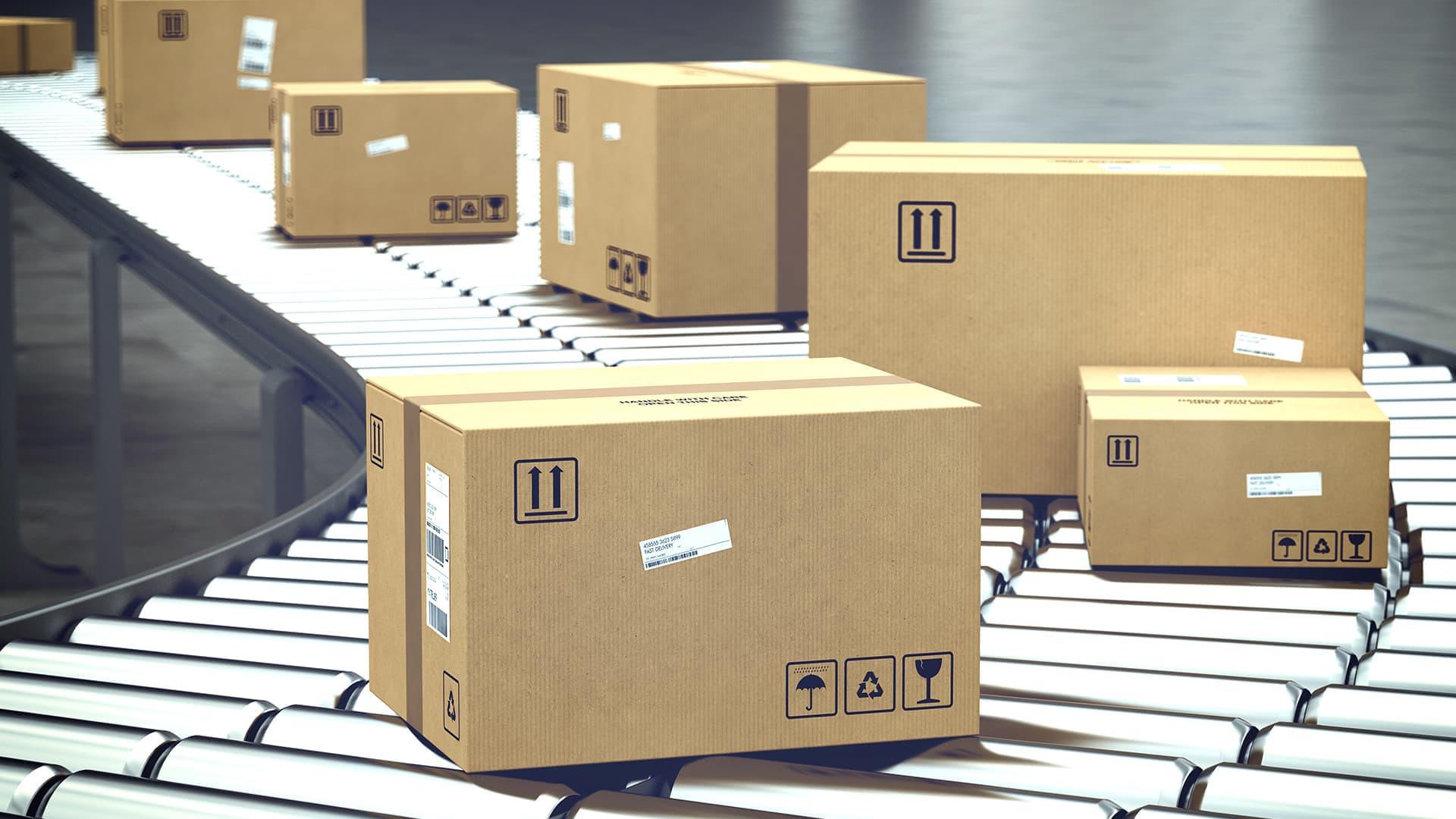
Top tips for shipping
- Get real-time inventory data and monitor outgoing shipments with a WMS.
- Use labour management systems to allocate resources effectively and evenly.
- Make the most of loading systems that give workers clear guidance on how to load orders quickly and safely.Optimise route planning and carrier selection with a
- Transportation Management System (TMS).
- Partner with a courier you trust to meet customer needs on time and without any damage.
Inventory tracking
Inventory tracking is a warehouse process that runs alongside almost all others. It involves recording and monitoring all the inventory in a warehouse, from receipt to delivery.
This is a crucial part of any logistics system as it helps prevent stock errors and ensures goods are ready for sale.
Back in the day, inventory tracking could only be done by manual counting – a time-consuming task prone to human error. Now, modern technology automates this process with smart software solutions that provide real-time inventory updates.
As a result, your warehouse can quickly identify any stock discrepancies or shortages.

Top tips for inventory tracking
- Standardise inventory management processes like receiving, putaway and picking to support more accurate tracking.
- Leverage automated systems to keep an eye on inventory levels and automatically reorder goods when they fall under a specific threshold to avoid running out of stock.
Get smart warehouse storage solutions in Sydney
A streamlined storage process for your warehouse is critical to operational efficiency. And ultimately, that means higher levels of productivity and customer satisfaction.
Ready to transform your facility?
As well as following the above procedures, you’ll need the right storage solutions.
Pallet racking is a key component of any warehouse. These strong, purpose-built structures make the most of valuable space, ensuring safe and secure storage.
Optimise the storage process in your warehouse with a robust pallet racking system. At Pallet Racking Sydney, we offer custom, cost-effective and durable storage solutions. Explore a full range, including Schaefer selective racking, cantilever racking, mesh, timber or steel longspan shelving and racking accessories.